The Problem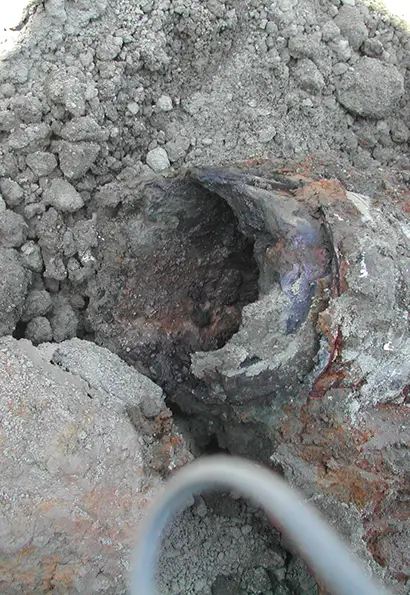
Former tenants of an industrial park in Fountain Valley had put a variety of chemicals and compounds down the drains during the life of the 50-year-old building. Photo developing fluids, metalworking chemicals, and more. Management realized the cast iron pipes were beyond their 40-year life expectancy and were failing. A 67-foot section of the 4” pipe was discovered to be missing. Something had to be done.
But the sewage drain line ran directly beneath the 500-foot-long single story structure, not offset into the adjacent alleyway or parking lot. Digging up and replacing the pipe was not a realistic option. No tenant wanted the floors of their reception areas and restrooms jackhammered, much less the mess and disruption of digging and removing quantities of dirt and corroded pipe.
![]() |
![]() |
![]() |
![]() |
The Solution
Mt. Baldy Office Park management reviewed several bids from plumbing companies that employ various methods and “high tech” processes to create and insert “a pipe within a pipe” without digging. San Diego Plumbing and Pipelining was chosen not only because of their expertise and knowledge of the various techniques but because of their “can do” attitude.
After examining the condition of the pipes with a sewer camera with a real-time video link, San Diego Plumbing and Pipelining chose to attack the problem by utilizing two different products: MaxLiner for the heavily corroded, 6” pipe in the lower portion nearer the front of the complex, and Formadrain for the longer upper portion where the camera revealed long sections of the original 4” drain pipe had actually deteriorated. Corrosion in the 6” pipe had narrowed the pas- sage to less than 4”.
Another factor in the choice of product was that the degree of slope changed at the same junction point. Code called for two degrees of slope, but the lower portion was only one degree. This condition caused greater buildup of corrosive matter in the lower section. With less slope, more solids and chemicals settle and deterioration accelerates.
In preparation, the San Diego Plumbing and Pipelining crew reamed out the entire sewer line with lengths of plumber’s snake followed by a high-pressure water jetter. Opening up the narrowed passage, how- ever, required more: a customized tool was needed. “Because of the heavy corrosion, we had to clean the pipe beyond what we do in our normal pipe lining projects,” San Diego Plumbing and Pipelining said. “Custom work on this job was needed. We created an abrasive high-speed (22,000 RPM) rotary cleaning tool. It is similar to what you need when you want to hone a cylinder on engine block prior to putting in a new piston. The technique was much more effective than sewer snakes and hydrojetting used by competitors.
MaxLiner
MaxLiner Lateral Lining Equipment was used in the lower section, a 108- foot shot. It consists of a felt liner tube with PVC coating, customized from 3 mils to 5 mils thick, and is an inversion process. That is, it is like taking a sock off your foot and turning it inside out. The process makes use of a resin to soak into the felt tube, to “wet it out.” The felt tube passes through
a roller to squeeze the resin along inside the tube.
Wetted and laid out like a fireman’s hose, the tube is fed into a MaxLiner “gun” that turns the tube inside out, and high pressure air pushes it down. To make it turn and slide easier, the tube is lubricated with liquid detergent. Wetted, the material is 4.5 to 5 mils thick. The resin is made of 4 parts resin base to 1 part resin hardener or catalyst.
After the full length of the wetted felt tube had been inserted, passed through the pipe and emerged at the exterior point of the building, an equal- ly long, Orange High Temp Calibration Hose was blown into the tube to make sure the felt material had inflated fully and conforms to the host pipe without wrinkles or tucks. The orange mate- rial was then withdrawn.
The resin normally hardens within four hours. On this job, San Diego Plumbing and Pipelining used a boiler to heat, pump, and recirculate water into the pipe to accelerate cure time. The High Temp Calibration Hose is designed to tolerate temps up to 180 degrees. It is made from a medium weight polyester fabric with PVC coating and is very tough.
Formadrain
San Diego Plumbing and Pipelining’s crew had a different solution for the upper half of the building. A section of the pipe had deteriorated – it was flat-out missing. The best product for the job was Formadrain. An 67-foot section of pipe was replaced with a rubber mandrel that, after being prepped and inserted into the line, was pulled in place and “popped” by high-pressure steam heat to 4” in diameter. Developed by Formadrain the “mandrel” (rubber sleeve used in the process) is small enough and of sufficient flexibility to be inserted into a standard cleanout, while having the ability to expand 200% in diameter, once injected with steam. It must also withstand steam pressure at 20psi.
For the Mt. Baldy job. two layers of cross-woven fiberglass mesh were prepared – a coarse, heavy layer for the outside of the replacement pipe, and finer mesh for a smooth finish on the inside, and wrapped around the mandril. This technique, which results in a “pipe within a pipe” even thicker and stronger than the felt tube liners, was called for because it had to span the areas of missing pipe.
This process called for blue resin and white hardener, a 50/50 mix, 16 lbs per bucket. Normally, ambient cure of this mix takes 4-10 hours, Use of a boiler to create steam and carefully regulating the pressure cut the time to 45 minutes. Unlike the felt tube, the process was a pull-in-place liner that conforms to the mandrel. The entire pipe is one single piece.