San Diego Plumbing and Pipelining uses industry-standard pipelining material resources and strictly adheres to technical specifications required by regulatory bodies.
Materials and technical specifications
- Resin: The resin we used is a 100% solid epoxy and hardener system specifically designed for the cured-in-place-pipe (CIPP) that is being installed.
- The resin shall be 15 base resin with the appropriate hardener. Pot life minimum is 16 minutes; pot life maximum is 75 minutes.
- The resin and liner system shall be ANSI/NSF 14 certified.
- The resin shall contain no styrene or other chemicals with severe odours.
- Liner material: The lining material for lateral pipes must provide the flexibility to line 45 and 90-degree bends that result in a finished liner with a smooth inside radius. It must be approved Formadrain® fiberglass, Maxliner/EasyLiner felt liners with and without reinforcement as part of the composite.
- Liners and bends to be lined include: Tubes of up to 22.5 degrees, i.e. fiberglass of up to 45 degrees, and cross woven fiberglass of up to 90 degrees.
- Proprietary materials and methods: Must meet ANSI/NSF Standard 14 consistent with ASTM F-1216 Standards; Uniform Plumbing Code and National Association of Sewer Service Companies.
Reference specifications
- Installation and material tests of cured-In-place-pipe (CIPP) must meet the minimum requirements demonstrated in the following ASTM standards:
- ASTM F-1216 Standard Practice for the Installation of Cured-in-Place Pipes
- ASTM D-638 Test Method for Tensile Properties of Plastics (Tensile Strength 3,000 psi)
- ASTM D-790 Test Method of Flexural Properties of Plastics (Flexural Strength 4,500 psi; Flexural Modules 250,000 psi)
Wastewater Collection Systems Maintenance and Rehabilitation- 10'r, Edition: Chapters titled "TV Inspection" and "Sewer Line Cleaning."
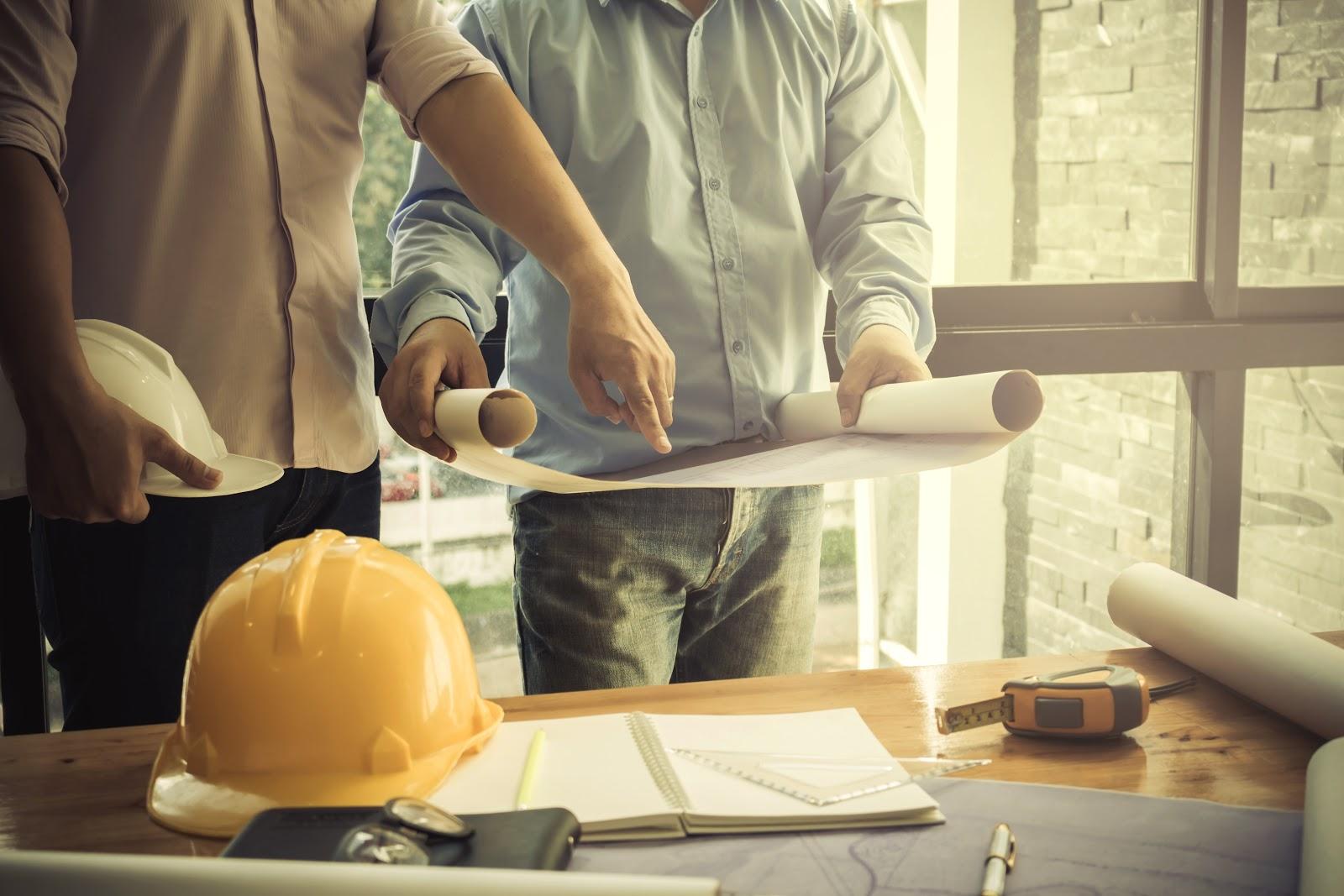
Prior to any pipeline construction work, a thorough site survey is conducted first along the proposed pipeline segment. The area is cleared, and utility lines, as well as agricultural drainage systems are identified and marked to prevent any accidental damage. The pipeline centerline and the boundaries of the exterior right of way are staked. Before any earth-moving activity commences, temporary soil erosion control measures are established. Topsoil is then removed and stored separately for later reinstatement.
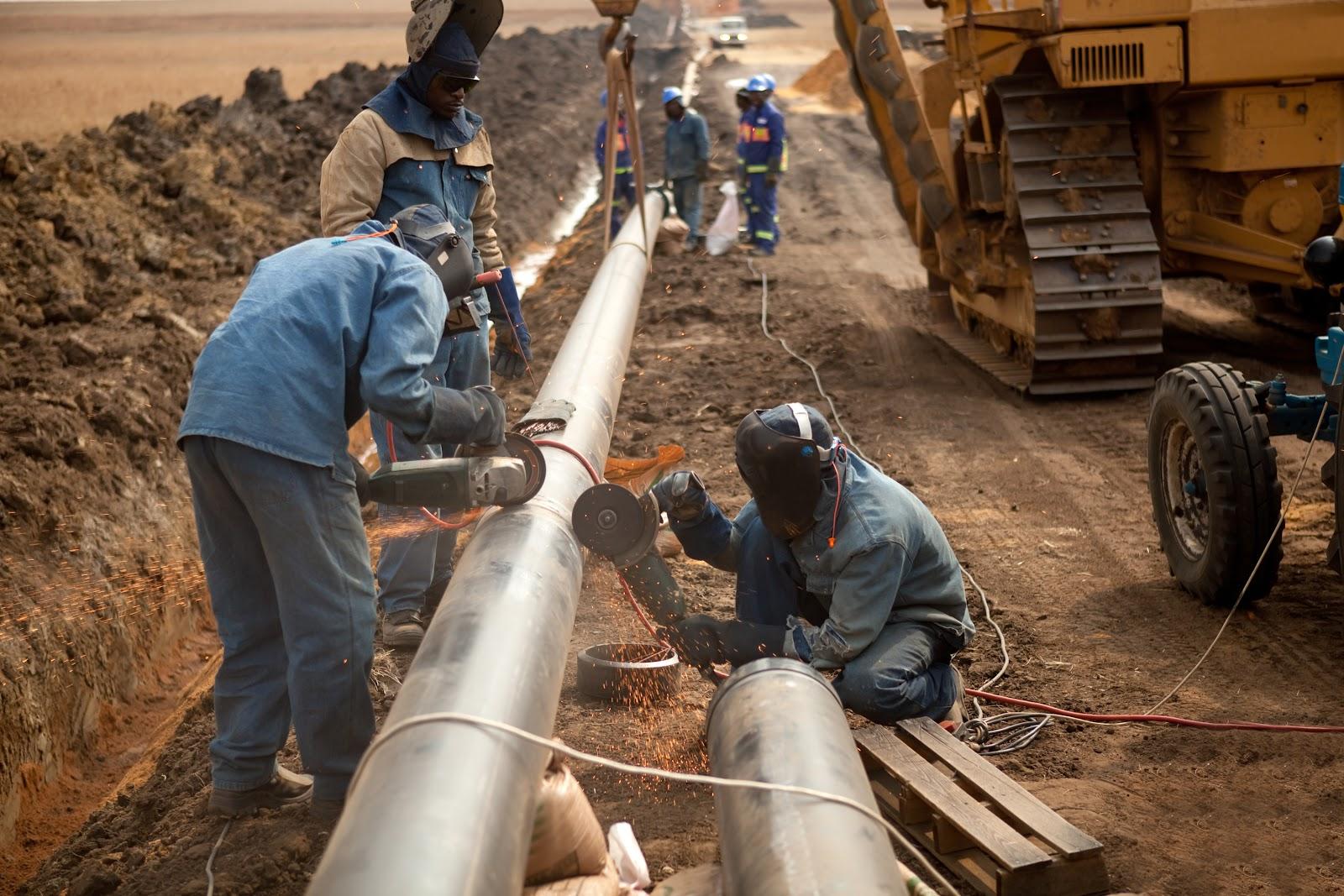
Individual pipe joints are strung along the trench. Then a mechanical pipe-bending machine is used to bend individual pipe joints at the required angle to suit the natural topography of the site. After stringing and bending work is done, pipe sections are aligned, welded together, coated (as needed), and inspected. Side-boom tractors are used to lower the finished pipes into the trench. After ensuring that no foreign materials are left in the trench, it is then back-filled completely.
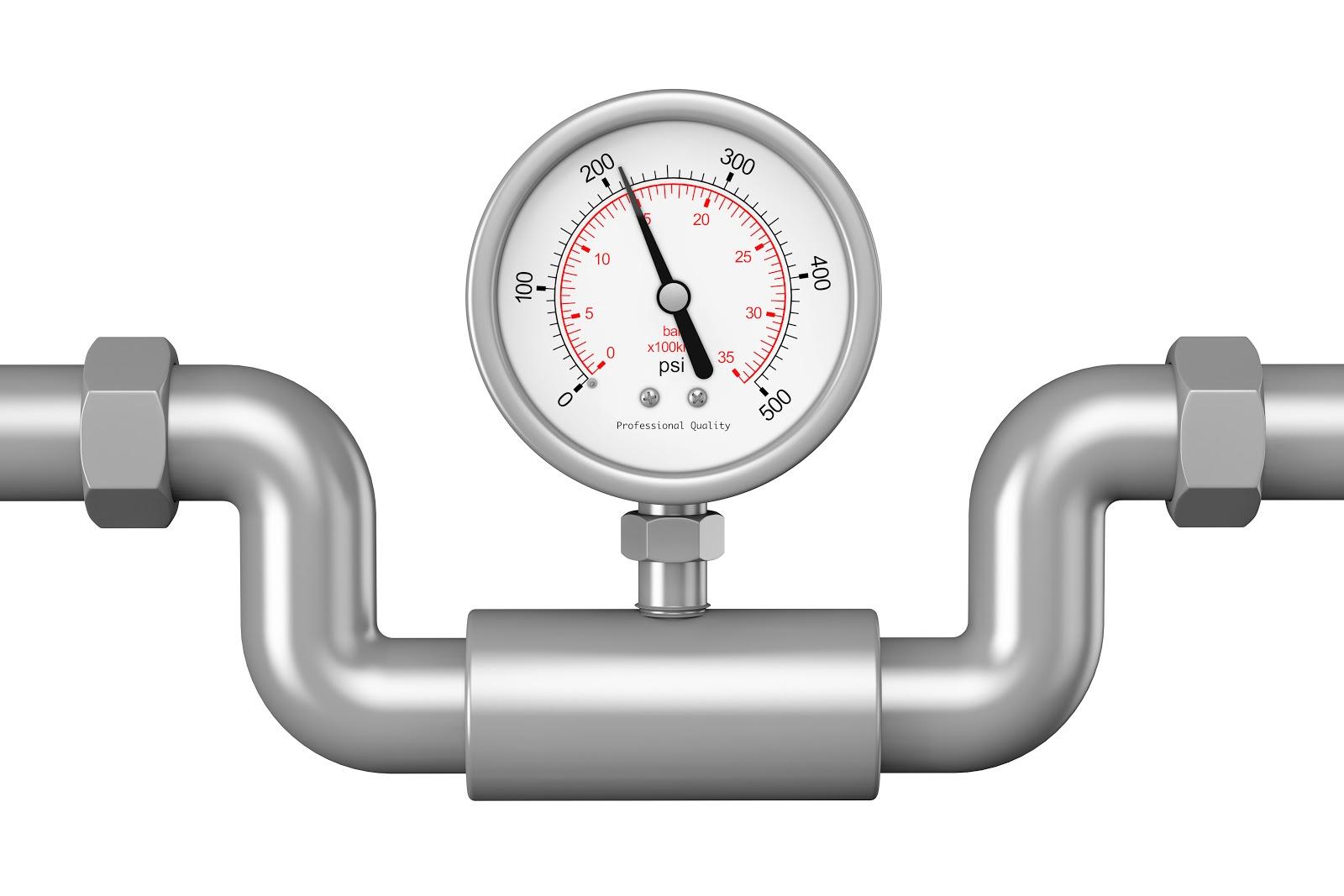
With the backfilling finished, the structural integrity of the pipeline is subjected to hydrostatic testing. The pipe system is filled with water which is then pumped at a pressure level that's higher than the maximum allowed for operating gas pressure. Afterward, the test water is disposed of in adherence to applicable federal, state and local regulations. All disturbed areas are restored, so the land looks as close as possible to its original appearance.
Call Today (855) ANY-PIPE or (855) 269-7473
Or fill in this form to get a free estimate
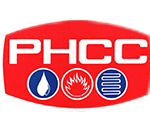
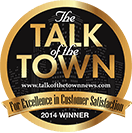
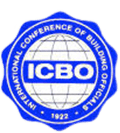